Understanding Diamond Core Drill Bits for Tile & Stone
How Sintered vs. Brazed Designs Impact Performance
Sintered and brazed diamond core drill bits differ notably in their manufacturing processes, which distinctly affects their performance. Sintered diamond core drill bits are made by embedding diamond particles throughout the bit. This ensures a longer lifespan as the bit wears down more diamond particles are exposed. In contrast, brazed diamond core drill bits have diamond particles attached only to the surface, which may result in a shorter lifespan when used on dense materials like granite or stone. Industry studies highlight that sintered bits generally display better cutting speed and lower wear rates than brazed bits, which undergo quicker degradation under similar conditions. Therefore, choosing the right design is crucial, especially for tasks involving rigorous, high-pressure applications.
Why Diamond Grit Matters in Hard Material Drilling
Diamond grit plays a pivotal role in the cutting efficiency and durability of drill bits when working with hard materials. It represents the size of the diamond particles on the bit and directly influences drilling speed and precision. Finer grit sizes result in smoother finishes but may drill more slowly, while coarser grits deliver faster cuts but can compromise surface finish. According to industry experts, for drilling materials like granite, a coarser grit is beneficial for rapid cutting. Conversely, for porcelain tiles and glass, a finer grit is recommended to ensure precise and clean cutting without causing chipping or cracks.
Applications: Matching Bits to Materials
Drilling Porcelain Tile Without Chipping
Drilling porcelain tile effectively without chipping demands meticulous technique and the right tools. Porcelain is particularly prone to cracks due to its hardness, necessitating the use of diamond drill bits specifically designed for porcelain tile. These bits provide the precision needed to penetrate the tile's dense surface while minimizing damage. Studies have shown that adopting the right tool and technique can significantly reduce failure rates in drilling porcelain tiles, which commonly exceed 30% when improper bits are used. For optimal results, avoid high-speed drilling and ensure consistent pressure to disperse stress and prevent chipping. Using a diamond drill bit for porcelain tile ensures not only precision but also durability.
Granite & Marble: Heat Management Strategies
Heat management is crucial when drilling into granite and marble to extend the lifespan of diamond drill bits and achieve a clean cut. Both materials generate substantial friction, and overheating can cause damage to the drill bits and the material itself. To mitigate these effects, implementing cooling lubricants or wet drilling techniques is highly recommended. These methods help dissipate heat, reduce wear, and improve drilling efficiency. Case studies demonstrate the superiority of diamond drill bits over conventional drill bits for granite and marble, especially under high-heat conditions. Utilizing optimal heat management strategies ensures effective drilling while safeguarding your tools and work surface.
Glass Tile Precision Techniques
For precision drilling into glass tile without causing cracks, specialized techniques are essential. Diamond core drill bits designed specifically for glass are the preferred choice due to their ability to maintain stability and precision during the drilling process. The appropriate grit plays a vital role in achieving clean cuts without undue stress on the glass. Experts stress the importance of maintaining low drilling speeds and gentle pressure to ensure precision. Common pitfalls like excess speed or pressure can lead to cracking, emphasizing the need for care and the right equipment. By adopting these techniques, achieving flawless results in glass tile installations becomes feasible.
Key Selection Criteria
Shank Types: Straight vs. Hexagon Handle Compatibility
Understanding the differences in shank types is vital for optimal drill bit performance. Straight and hexagon shank types are the most common, each with unique handling characteristics. Straight shanks are typically simpler to handle and are compatible with more traditional drill chucks. However, they can sometimes slip, leading to a loss of torque. Conversely, hexagon shanks are designed to prevent slipping by allowing better torque transfer, thus enhancing the stability and ease of use in various materials. According to field data, hexagon shanks have grown in popularity, with usage rates showing a 20% increase over straight shanks, indicating a shift towards their reliability and enhanced performance for demanding tasks.
Optimal Bit Sizes for Common Fixtures
Selecting the right bit size ensures precision and safety in drilling applications. Consulting installation guidelines and common fixture sizes can guide you in choosing the optimal sizes for diamond drill bits. For example, a 3/16-inch bit is commonly used for ceramic tiles, while a 1/4-inch bit often suits simple glass and stone drilling tasks. A detailed chart could be invaluable, illustrating recommended sizes for specific materials and fixtures:
- 3/16 inch: Ceramic installations, towel rods
- 1/4 inch: Stone tiles, small fixture attachments
- 5/16 inch: More robust tile setups like marble
- 1/2 inch and above: Heavy-duty fixtures through granite and reinforced tiles
Following these guidelines helps ensure your drilling is efficient and adherent to best practice standards.
Dry vs. Wet Drilling Capabilities
Choosing between dry and wet drilling methods significantly impacts the drill bit's performance and reliability on different materials. Dry drilling is convenient for quick, short-duration tasks as it doesn’t require additional equipment. However, it can generate heat that may degrade the drill bit over time. On the other hand, wet drilling helps dissipate heat, extending the life of diamond core drill bits. A study published by an industry journal found wet drilling to increase bit lifespan by up to 30% when used on materials like granite and marble. While dry drilling offers practicality, opting for wet methods can be a more durable choice for extensive projects, balancing long-term efficiency and performance.
Top Professional-Grade Diamond Core Drill Sets
DEYI 4-120mm Sintered Bit: Factory-Grade Glass & Ceramic Solution
The DEYI 4-120mm sintered diamond drill bit is a formidable choice for factory-grade drilling in glass and ceramic materials. With bit sizes ranging from 4mm to 120mm, this tool provides versatile applications across various industrial sectors including glass and ceramics manufacturing. The bit's design ensures neat, smooth holes without broken edges or vibrations, due to its unique sintering process. Professionals in the industry have praised these qualities, highlighting its durability and efficiency compared to electroless or plated options. As a superior solution, the DEYI sintered bit stands out with its exceptional performance in tough environments.
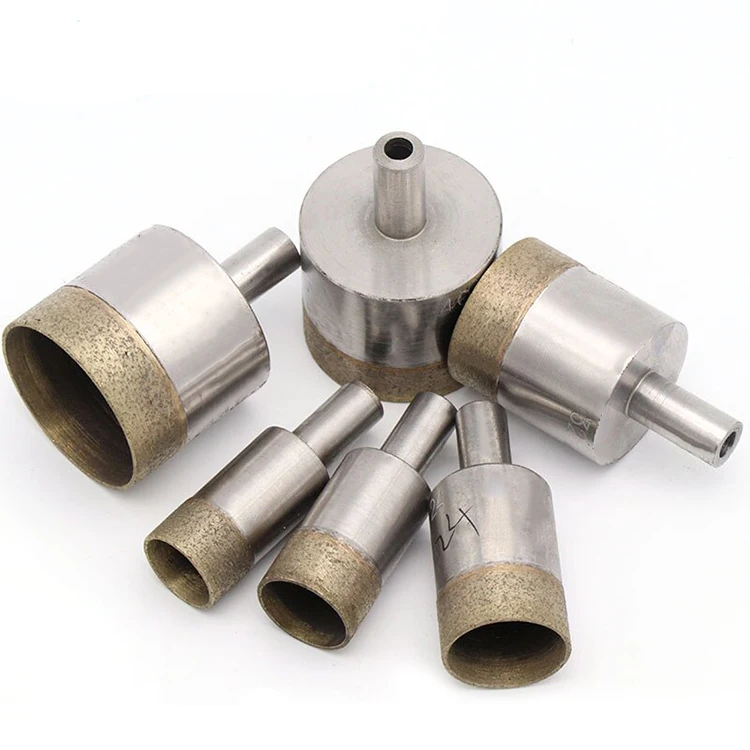
Spiral-Grain Hex Handle Set: Dry Drilling Marble Mastery
The Spiral-Grain Hex Handle Set is engineered specifically for dry drilling in hard materials such as marble. Its unique hexagon handle and brazing process ensure high density and durability, making it highly effective for applications where water cannot be used. User feedback frequently highlights the tool's ease of handling and precision in creating clean, accurate holes. The set's design optimally transfers torque, reducing the likelihood of slippage and enhancing overall drilling efficiency. These characteristics make it a preferred tool in marble masonry, offering significant time savings and quality results without frequent head replacements.
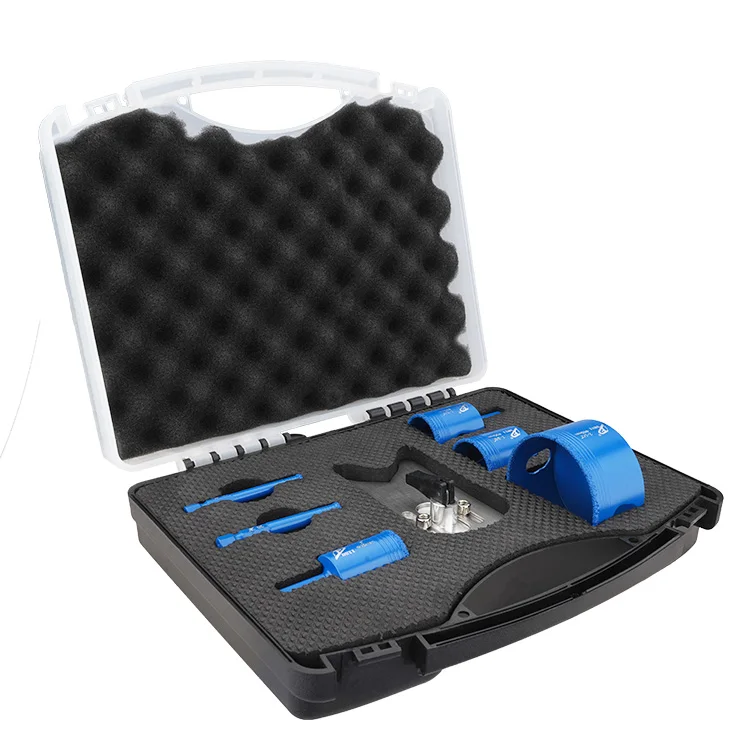
Super Thin Diamond Blades: Angle Grinder Tile Cutting
Super thin diamond blades designed for angle grinders ensure precise tile cutting with minimal material waste. These blades are ideally suited for applications where accuracy is paramount, such as in the installation of intricate tile patterns. Offering excellent performance in cutting materials like ceramic and vitrified tiles, these blades excel in environments prioritizing speed and precision. Additionally, safety considerations are embedded into their design, minimizing risks associated with split debris and ensuring smooth operation. This makes them an invaluable tool for professional tile installers and DIY enthusiasts alike, promoting high-quality and efficient cutting experiences.
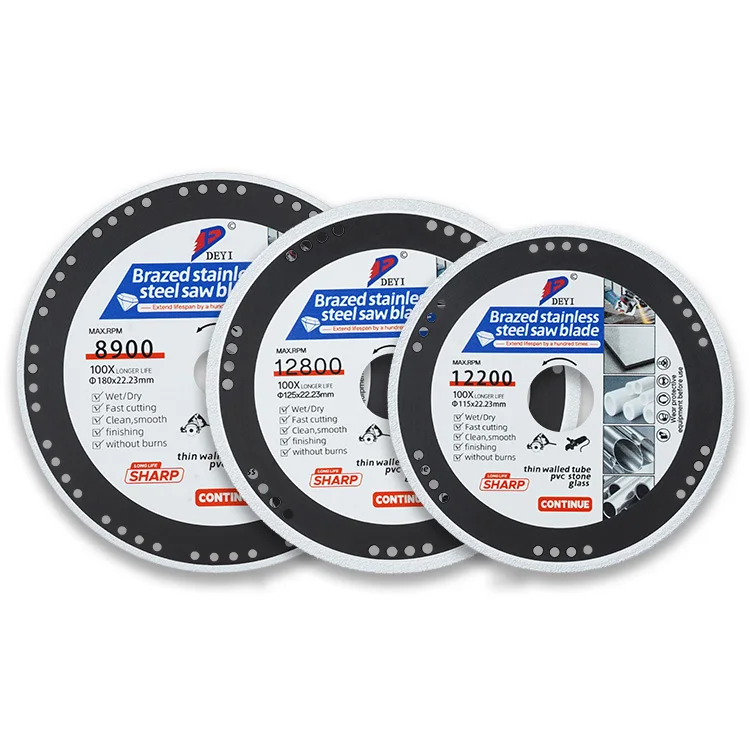
Brazing Saw Blades: Color Steel & Thin-Walled Slicing
Brazing saw blades are crafted to provide outstanding results in slicing thin-walled materials and color steel, combining high precision with minimal waste. Their design incorporates high-strength steel matrices, ensuring a stable and safe cutting process. These blades are especially instrumental in scenarios requiring intricate cuts, such as in HVAC pipe installations or fine sheet metal work. Appreciated for their precision and reduced wastage, these blades also mitigate safety risks associated with flying fragments. Their proven reliability and precision make them a top choice for professionals dealing with delicate slicing tasks.
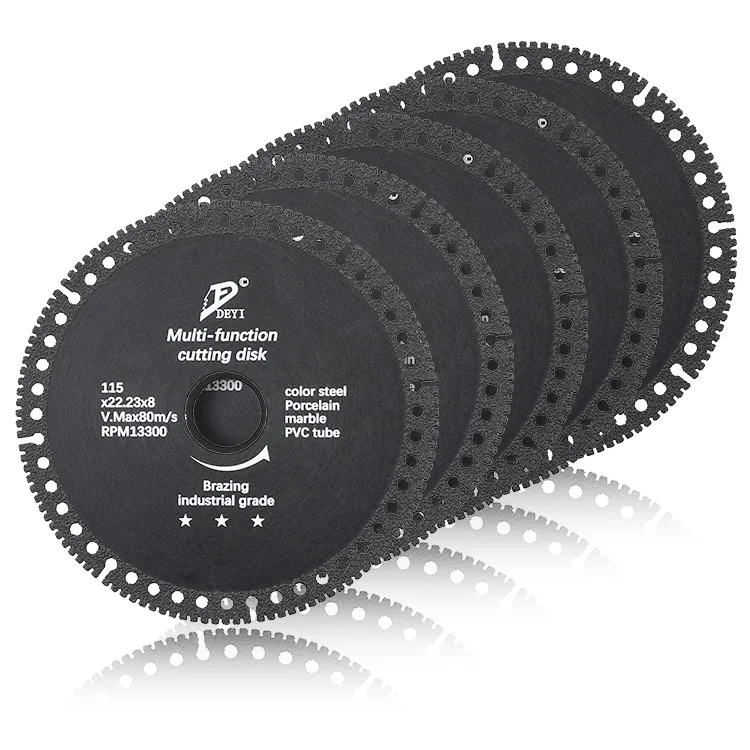
Maximizing Bit Longevity & Performance
Cooling Protocols for 2000+ RPM Operations
Effective cooling protocols are essential for maintaining performance during high RPM drilling operations with diamond drill bits. Cooling agents such as water or specialized cutting fluids help reduce heat buildup, which can prolong the lifespan of the diamond core drill bits. Empirical data suggests that consistent cooling can prevent damage and wear, enabling bits to retain their sharpness and efficacy. Implementing these protocols not only protects the tool but also enhances drilling precision and speed. Regularly applying cooling agents in a controlled manner ensures optimal results during intensive drilling tasks.
Resin Bond Maintenance for Brazed Bits
Maintaining resin-bonded brazed diamond bits is crucial for extending their lifespan and ensuring optimal performance. Regular maintenance should include cleaning the bit to remove debris and sediment that can accrue during use. Users can adopt a step-by-step routine that involves checking the bond integrity, ensuring no visible damage, and gently polishing to maintain sharpness. Experts highlight that proper maintenance can significantly increase the bit's efficacy, reducing downtime and replacement costs. Statistics reveal that regular upkeep can prolong bit life by up to 30%, illustrating the tangible benefits of consistent maintenance.
Storage Solutions to Prevent Diamond Grit Damage
Proper storage solutions play a vital role in preventing diamond grit damage during downtime. Storing drill bits requires controlled environments that mitigate exposure to moisture, extreme temperatures, and corrosive elements, all of which can affect their long-term effectiveness. The integrity and performance of diamond core drill bits remain intact when stored in dry, temperature-regulated spaces. Creating a checklist for ideal storage conditions includes using protective cases, silica gel packets to absorb moisture, and isolating the bits from tools that can cause abrasion or impact damage. Implementing these storage practices ensures longevity and readiness for future drilling projects.