Understanding Diamond Cutting Technology
The Science Behind Diamond Tool Durability
Diamond tools are renowned for their exceptional durability, which is largely attributed to the crystalline structure of diamonds. Diamonds, with their tightly bonded carbon atoms, rank as the hardest natural material, ensuring tools crafted with this stone exhibit remarkable hardness and resilience. Several factors, such as bond types and grit sizes, significantly influence the longevity of diamond tools. For instance, the choice of a metallic bond can enhance tool life but may compromise cutting speed compared to resin bonds. According to the scientific analysis, diamond tools show a lifespan up to 50% longer than traditional tools, owing to their superior composition and design.
Types of Diamond Tools for Masonry Projects
In the realm of masonry, a variety of diamond tools are available, each suited to specific tasks. These include diamond saw blades, drill bits, and grinding wheels. Diamond blades are ideal for precise cutting of concrete, marble, and granite, offering unparalleled accuracy and speed. Diamond drill bits, particularly used for glass, granite, and porcelain tiles, provide precision and efficiency in creating holes without damaging the material. Grinding wheels are essential for smoothing and shaping surfaces, which is crucial in masonry work. Innovations in diamond tool technologies have been spearheaded by brands such as DEYI Diamond Products Co., Ltd., which lead in usability and effectiveness. Their advancements enable professionals to execute tasks with greater precision and efficiency, directly impacting project outcomes.
Key Features of Professional-Grade Diamond Tools
Heat Resistance and Longevity in Cutting Tools
Heat generation is a major factor affecting not only the performance but also the lifespan of cutting tools. When diamond drill bits and saw blades are employed, they often face intense friction, which elevates operational temperature and risks tool degradation. To combat this, modern manufacturing processes have incorporated various heat resistance technologies. For instance, advanced binding agents and alloys are used to dissipate heat effectively, prolonging the tool's life and ensuring consistent performance. Companies focusing on superior heat management technologies have demonstrated increased longevity in their diamond cutting tools. This innovation not only enhances the tool's robustness but also reduces maintenance costs and downtime, offering a clear advantage over competitors.
Precision Engineering for Clean Cuts
Precision engineering is crucial in the development of diamond tools, ensuring clean and precise cuts across various materials. This meticulous approach involves detailed design and manufacturing processes that consider minute tolerances and high precision in crafting tool surfaces. The impact of precision is evident in the quality, efficiency, and finish of cuts, particularly when working with materials like porcelain tiles and granite. For example, studies have shown that precision-engineered diamond core drill bits significantly outperform traditional methods, offering smoother results and faster processing times. This showcases the importance of advanced engineering in achieving optimal cutting quality, which is essential in high-stakes projects demanding perfection.
Specialized Applications in Construction Materials
Optimizing Concrete Cutting Performance
Concrete cutting presents unique challenges that demand specialized tools. Diamond tools are preferred for their ability to effectively cut through tough concrete surfaces, owing to their durability and superior cutting performance. Utilizing the right diamond blade is crucial, as it must match the specific hardness and composition of the concrete. Configuration of the tool, such as choosing the appropriate blade and adjusting the revolutions per minute (RPM), is essential for optimizing performance. Experts recommend specific tool setups depending on the concrete's density. For instance, a low RPM setting and a high-grade diamond blade are suggested for cutting through dense concrete, maximizing efficiency while minimizing wear on the tool.
Marble Processing Techniques with Diamond Tools
Marble processing requires meticulous techniques to ensure precision and avoid damage. Diamond tools excel in this domain due to their ability to deliver clean cuts and superior polishing results. Selecting the appropriate tool and operating settings is vital to maintain the integrity of the marble surface. Employing advanced technology, such as water-cooled diamond blades, can prevent overheating and ensure smooth cuts. Industry best practices also emphasize the importance of slow, steady cutting speeds to enhance precision and reduce the risk of chipping. By leveraging these advanced techniques, professionals can achieve immaculate results while preserving the natural beauty of marble.
DEYI Diamond Tools: Premium Solutions for Precision Work
Electroplated Diamond Hand Polishing Pads (50#-400#)
Electroplated diamond polishing pads are essential tools for achieving premium finishes on stone materials. These pads range between 50# and 400# grit, ensuring versatility across various surfaces such as concrete, glass, and stone. The electroplated diamond technology enhances durability and precision, eliminating inefficiencies in polishing. Users report significant improvements in finish quality when using these pads, as demonstrated by various case studies where the pads were applied efficiently to refined stone surfaces, highlighting their reliability in diverse applications.
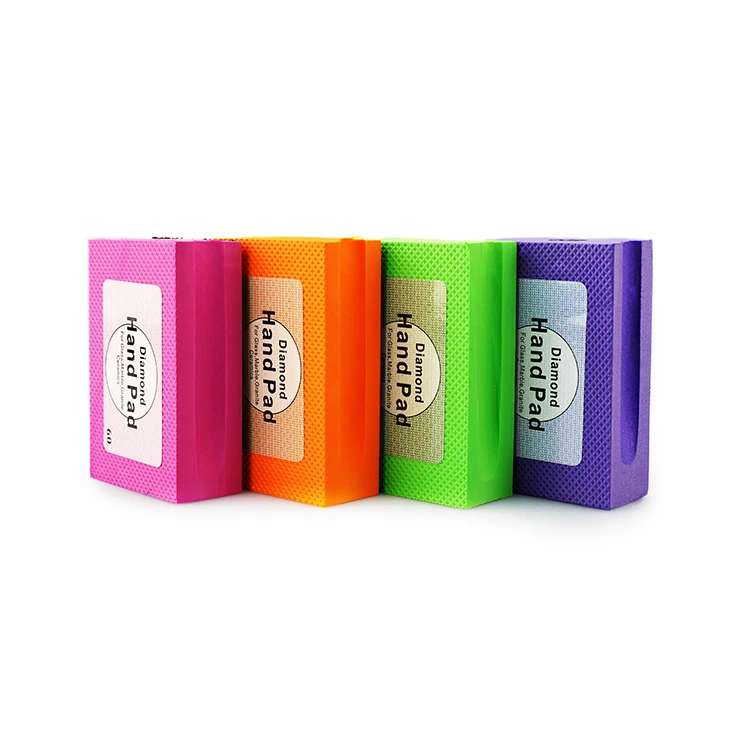
Dry/Wet Diamond Polishing Pads for Natural Stone
Understanding the difference between dry and wet diamond polishing pads is crucial for optimal natural stone finishes. Wet polishing pads typically offer more control over dust particles and are ideal for marble and granite, enhancing both safety and results. In contrast, dry pads achieve quick surface touches, often preferred when water use poses a constraint. Selecting the appropriate pad requires consideration of the stone's hardness—a necessary step to avoid potential damage. Regular maintenance ensures prolonged pad effectiveness, involving routine cleaning and correct storage to preserve their high performance.
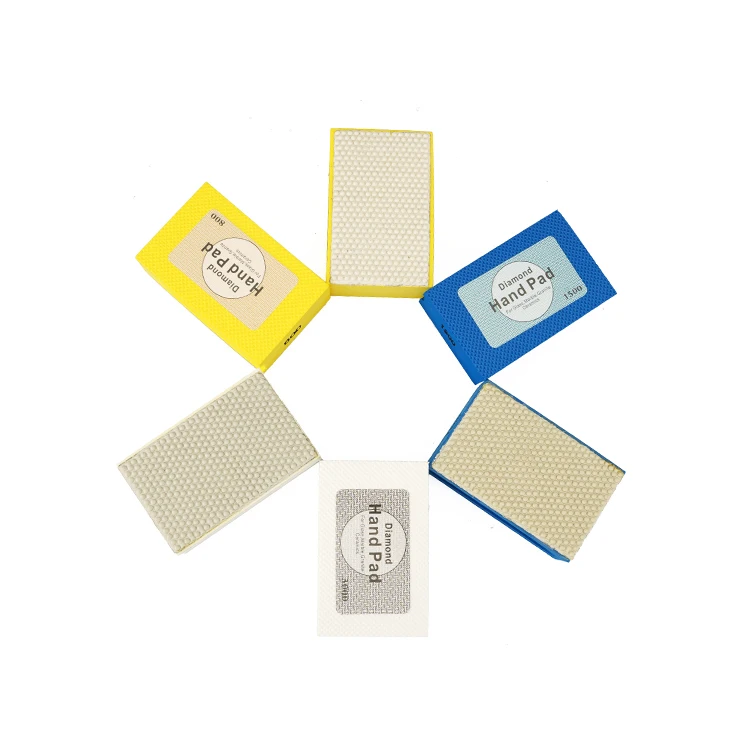
Extreme Sharpness Diamond Drill Bits for Glass and Tile
DEYI's sharp diamond drill bits are specifically engineered to handle the delicate materials of glass and tile without causing chipping or cracks. Their precision-crafted design ensures optimal performance, essential for operations requiring high accuracy. Correct bit selection is crucial; using subpar options risks damaging these brittle surfaces. Industry players favor best practices, such as maintaining steady pressure and slow drilling speeds, ensuring effective outcomes and prolonging tooling lifespan, especially for intricate glass and tile jobs.
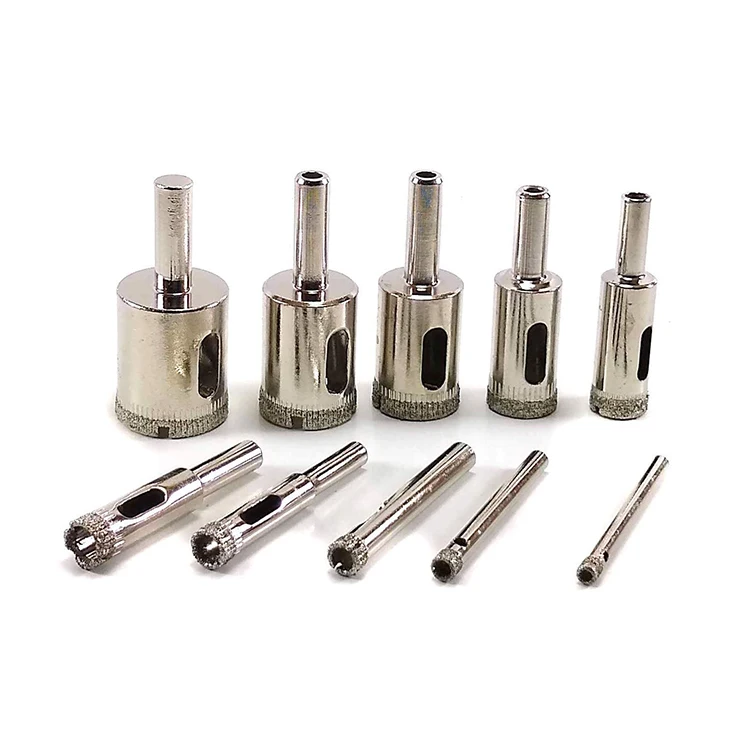
Vacuum Brazed Profile Grinding Wheels
Vacuum brazing technology offers enhanced durability in the production of diamond profile grinding wheels. This technique imbues wheels with long-lasting cutting edges, suitable for complex shapes in materials such as marble, granite, and porcelain tiles. These wheels are highly effective in detail-oriented applications where precision is necessary to achieve specific profiles. Vacuum brazed wheels demonstrate remarkable performance on a diverse range of construction materials, consistently maintaining smooth finishes and shape integrity.
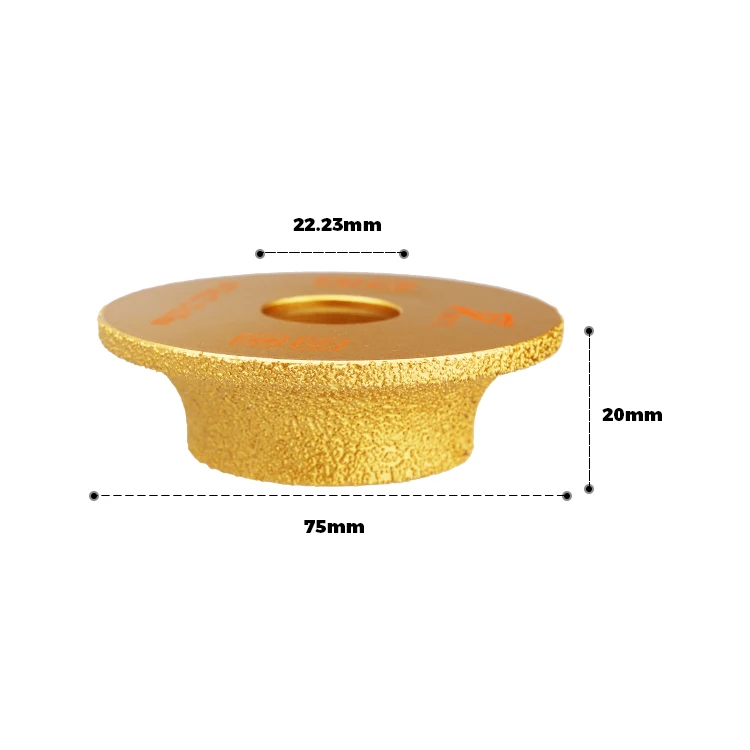